加工钼用什么数控刀片(钼的车削怎么加工)
钼合金的强度、硬度均较高,韧性差,性脆易折断,可加工性差,但因其具有熔点高、密度低和热 胀系数小的特性,常用于制造航空和航天的各种高温部件。两种钼合金零件分别为钼螺钉和钼螺栓,如附图所示。毛坯来料为热轧Ф16mm钼合金钢棒,加工中发 现该材料密度低,表皮硬度非常高,应为退火残余硬度。表层以内硬度仍然很高,韧性差,导热慢。使用普通高速钢或硬质合金刀具加工非常困难。首先,刀具前、 后刀面及刀尖磨损很快,加注切削液,使用常态下不同切削用量多次试验,均无法获得满意效果,一般外圆刀片加工不过4件就需更换;其次,零件在刀具稍有磨损 时即出现掉渣缺陷,平端面、切断及车螺纹时均出现掉渣现象。外圆加工及端面加工在精车刀保持锋利情况下可基本满足图样要求,但螺纹加工掉渣始终无法避免。
在实际加工中M6螺纹车制效果较差,加工中常发生螺纹段从收尾处折断现象,无法避免。只有采用板牙加工。M12则采用数控车高速双刀车螺纹,效果非常理想。
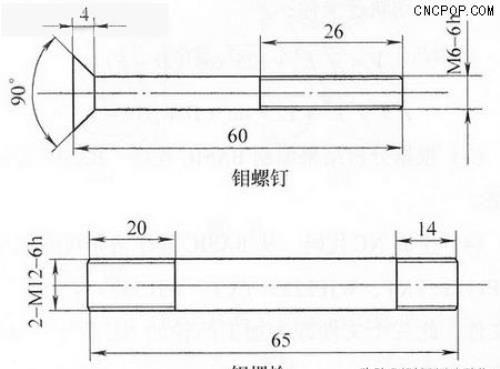
由于两种零件均较长,因此实际加工中,一般把车螺纹工步放在车外圆→切断→平总长加工完最后进行。由于工艺文件中M6螺钉、M12螺栓均不允许留有中 心孔,因此卧式车床加工中最后还需把中心孔平掉。数车加工中采用分段加工的办法,不钻一中心孔。分段加工Ф12mm外圆(M12大端直径)→切断;分段加 工Ф6mm外圆(M6大端直径)→车锥而→切断。程序较为简单,在此略去。需注意的是Ф6mm外圆尺寸加工至Ф5.85~Ф5.93mm时,明显有利于套 制螺纹。外圆大于Ф5.93mm则套制余量大,易发生螺纹掉渣、缺螺纹等牙型不完整现象。外圆小于Ф5.85mm则套丝时挤压变形量有限,如机床尺寸发生 波动,易使M6螺纹大端尺寸接近极限或超差。另外切断时,总长留量需大于1.5mm以上。以防切断刀变钝或排屑不畅挤压,使零件根部锥面(螺钉)掉渣,在 平完端面后也无法修复。亦即平完端面后零件仍有掉渣缺陷。
加工这两种零件外圆及总长时,普通硬质合金刀具的材料牌号选用YG6或YG8,磨制角度可参照不锈钢半精加工刀具角度磨制,如有条件采用机夹刀加工、 使用涂层刀具效果较好。涂层刀具一般分为物理气相沉积(PVD)和化学气相沉积(CVD)。与传统硬质合金刀具相比,涂层刀具强度、硬度、耐磨性有很大提 高。对硬度55HRC以下材料可实行高速切削,在对该两种零件外圆加工时(PVD)或(CVD)均可,使用(CVD)刀片略好。
切削用量:转速600~900r/min。背吃刀量0.3~0.6mm。进给量0.2~0.3mm/r。由于产生的切削热很大,加工时使用以冷却为主的水溶性切削液。
加工完外形及总长尺寸后,即要开始加工螺纹,在加工M6-6h螺纹时,卡盘定心须准确。尽量不要使用板牙架,用套丝器加工较好,因材料硬、脆。板牙架 夹持板牙的中心线与工件中心线稍有偏移,零件就极易折断或掉渣。套丝器则可适当补偿二者中心线的偏差,套丝时采用以润滑为主的切削油工业用豆油。
在加工M12-6h螺纹时,由于套丝加工时扭矩大,不易夹紧,导致工件打转。更严重的是,由于材料的特殊性,螺纹会产生严重掉渣缺陷,牙型不完整。使 用板牙无法加工出合格的产品。在卧式车床上使用螺纹刀车螺纹,采用高速钢(W18Cr4V)刀具切削,使用低速(50r/min)加工,很快达到刀具磨损 极限,切削效果也非常不理想。而在数车上采用硬质合金YG8,YG6,YW1等焊接刀具及涂层刀具PVD,CVD使用1200r/min以下各转速试验, 效果也均不理想。
针对实验结果及材料特性,决定使用国际上新的加工理论——高速、快走、小吃刀切削法试验。针对材料特性及刀具磨损情况,车螺纹采用难度较大的高速(2100r/min),双刀分粗、精车法加工。经过对螺纹加工指令格式的比较,首先淘汰了G34(变螺距螺纹指令)和G32(单一螺纹切削指令,进退刀 须另外指定,太繁琐),决定使用G92和G76编程分别试验。加工程序如下:
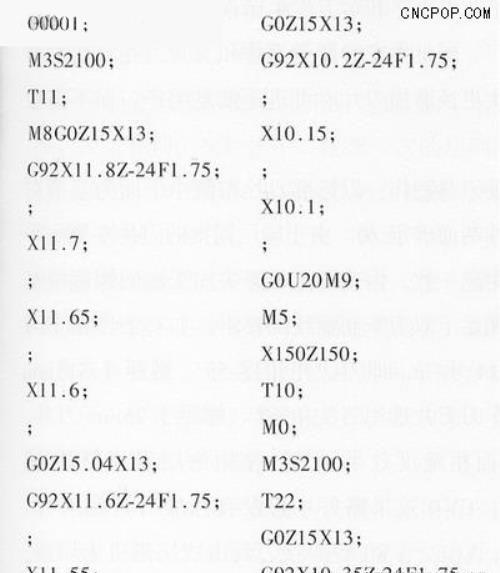
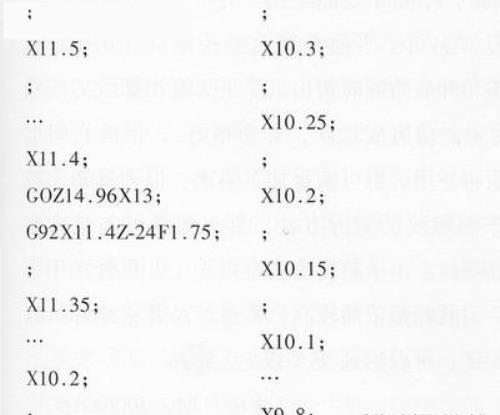
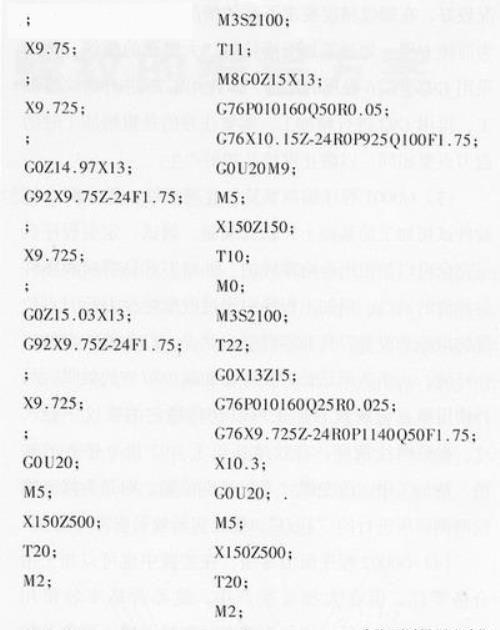
加工中,粗加工1号螺纹刀使用以冷却为目的的水溶性切削液;精加工2号螺纹刀工作时使用以润滑为目的的工业用豆油,用毛刷蘸抹。
编程说明:
(1)以上两个程序O0001和O0002是基于发那科0—T系统编制,O0001程序中间即使省略了很长一段,仍可看出用G92编程远远繁琐于用G76编程。
(2)两种螺纹切削循环指令格式特点:G92螺纹切削循环采用直进式进刀方式,由于刀具两侧刃同时切削工件,切削力较大,而且排屑困难,因此在切削 时,两切削刃容易磨损。在切削螺距较大的螺纹时,由于切削深度较大,刀刃磨损较快,从而造成螺纹中径产生误差。但由于其加工的牙型精度较高,因此一般多用 于小螺距、高精度螺纹的加工。由于其刀具移动切削均靠编程来完成,所以加工程序较长。由于刀刃在加工中易磨损,因此在加工中要经常测量。
G76螺纹切削循环采用斜进式进刀方式,由于单侧刀刃切削工件,刀刃容易损伤和磨损,使加工的螺纹面不直,刀尖角发生变化,而造成牙型精度较差。但由 于其为单侧刃工作,刀具负载较小,排屑容易,并且切削深度为递减式,因此,此加工方法一般适用于大螺距、低精度螺纹的加工。此加工方法排屑容易,刀刃加工 工况较好,在螺纹精度要求不高的情况下,此加工方法更为简捷方便。如果需加工高精度、大螺距的螺纹,则可采用G92、G76混用的办法,即先用G76进行 螺纹粗加工,再用G92进行精加工。需要注意的是粗精加工时的起刀点要相同,以防止螺纹乱扣的产生。
(3)O0001程序编制繁复,容易出错。但在配合试验件试切加工的基础上,认真编制、调试、定型程序后是完全可以加工出合格零件的。针对刀具易磨损 和零件易掉渣的缺点,粗加工程序中通过改变螺纹刀起刀点位置的措施来改变刀具和零件受力状况,以改善二者的工作环境,从而达到延长刀具寿命和减少掉渣的效 果。另外使用第二把螺纹刀加工可以获得稳定的螺纹中径尺寸,保证螺纹精度,有效地补偿了G92指令格式的缺憾。精加工中,改变螺纹刀起刀点位置,则是为修 光螺纹两侧面所进行的“赶刀”,螺纹实际效果非常理想。
(4)O0002程序简洁易编,在实践中也可以加工出合格零件。但在大批量生产中,成品合格率较使用O0001程序加工低,主要表现在时有轻微掉渣现 象及螺纹两侧面表面粗糙度稍差。分析原因是由于G76指令格式特点决定的,尽管同样使用两把刀分粗、精车来避免刀具磨损对螺纹尺寸精度的影响,G76格式 却不能进行重复上一刀尺寸的加工,也就是我们车削加工中常说的“圆整”加工简称“圆刀”,而在该零件的加工中,却必须进行“圆刀”,否则掉渣现象比较严 重。尽管G76指令格式的“斜进法”进刀方式能改善工件和刀具的受力状况,减轻工件掉渣现象,但不能根本杜绝掉渣,而在精加工中进行的为提高螺纹表面质量 所必须的“赶刀”G76格式也很难进行。因此O0002程序被放弃。
而用G76编制粗加工程序,用G92编制精加工程序的方法效果也不佳。因粗加工中时有发生的掉渣现象,到精加工时无法修复。会产生牙型不完整缺陷,将导致零件报废。故在实际加工中使用O0001程序。
程序简介:
(1)零件X向尺寸衔接。在粗加工中刀具已加工到X11.1,而精加工却从X11.3开始进刀,是考虑到对刀误差、粗车刀磨损等情况而预留的余量,因此在粗、精车刀未磨损、对刀准确的情况下,精车刀开始几刀是不切削的,可用来为工件毛刷蘸抹豆油做好准备。
(2)起刀点定在Z15开始,是因机床转速及刀架快移速度很高,必须给编码器足够的反应时间,使机床在转速及螺旋线轨迹在达到没定值时才开始进行螺纹 插补。开始试制时螺纹刀起刀点为Z5。但在自检时发现在螺纹中径尺寸已达到公差下限,且在螺纹全长上螺纹大径和中径无锥度情况下,环规旋人至第三、四个螺 纹时,明显有突然‘发涩’现象,而通过该点后,则旋入非常松快。经分析原因后,将起刀点值改为Z15后,现象消失。即使在刀具磨损,螺纹中径值在刚进公差 0.05mm时环规旋人还很轻松。
(3)提高效率,减少单件工作时间。在退刀U20后即提前指令停止主轴运转,设定M5。在刀架退到远离工件时,主轴已基本停止,即可开始检测,装卸工 件了。检测时以环规为主,每件检测螺纹综合尺寸,用环规通、止端保证。每5件以螺纹中径千分尺测量中径前后差值,掌握刀具磨损情况。加工20mm螺纹一头 时,装夹时工件伸出卡盘长度为26mm,以工件端面为程序原点埘刀确定Z0,加工另一头14mm,螺纹时,只需把工件仲出长度改为20mm即可开始加工, 不需重新对刀,从而避免了改编程序和对刀发生错误的可能性。如有条件选用同厂、同批生产的两个刀体和刀片,在初次对刀后,在每次更换磨损刀片时可迅速恢复 牛产,而不需重新对刀。
对刀及刀具制作:以标准刀片左侧小平而为基准对刀,以工件端面确定Z0。由于同厂同批的刀片左侧小平面与刀尖距离一致,因此两把刀刀尖加工出的螺旋线 是重合的,满足了双刀车制螺纹的要求。如有条件粗车刀刀片选用14牙/in,即刀尖角角度55°、螺距1.815mm刀片,精车刀刀片选用刀尖角60°、 螺距1.75mm刀片,则螺纹表面粗糙度效果更好。使用涂层刀片PVD或CVD均可,CVD效果略好。若没有标准刀具和刀片,可用YG8、YG6、YW1 等焊接刀具由线切割机床切制,在刀尖左侧约1.5mm处加工出一小平面,用于对刀。粗、精车刀刀尖与小平面距离公差控制在±0.01mm,螺纹刀刀尖角和 后角同时切出。手工刃磨出螺纹刀前角(大圆弧前角,切屑成球状,寿命稍好),用油石研磨前、后角后再使用,也可满足加工要求,但刀具寿命较差。
免责声明:本文内容由互联网优秀作者用户自发贡献,本站仅提供存储空间服务,不拥有所有权,不承担相关法律责任。若有涉嫌抄袭侵权/违法违规的内容,请与我们取得联系举报,一经查实立刻删除内容。本文内容由快快网络小信创作整理编辑!