机器人焊接缺陷产生的原因及其防止措施一般包括(导致机器人焊接缺陷的原因有哪些)
导语:机器人焊接缺陷产生的原因及其防止措施,一定要收藏
机器人焊接缺陷的分类
一、机器人弧焊焊接缺陷的分类
1.焊缝外观缺陷
(1)咬边 咬边是指沿着焊趾,在母材部分形成的凹陷或沟槽,它是电弧将焊缝边缘的母材熔化后没有得到熔敷金属的充分补充所留下的缺口,如图1所示。
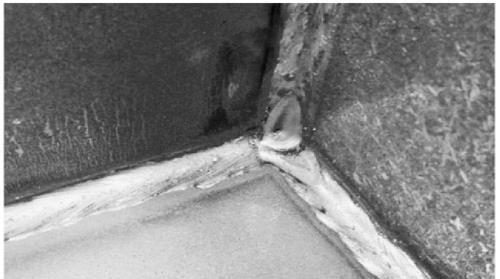
图1
(2)焊瘤 焊缝中的液态金属流到加热不足未熔化的母材上或从焊缝根部溢出,冷却后形成的未与母材熔合的金属瘤称为焊瘤,如图2所示。
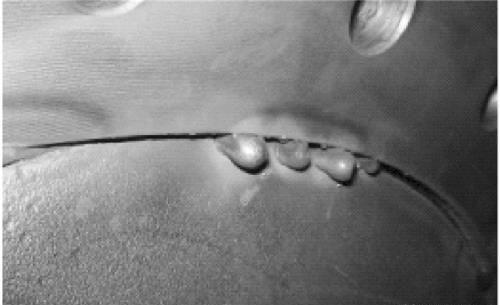
图2
(3)烧穿 烧穿是指焊接过程中,熔深超过工件厚度,熔化金属自焊缝背面流出,形成穿孔性缺陷,如图3所示。焊接电流过大,焊接速度太慢,电弧在焊缝处停留过久,都会产生烧穿缺陷;工件间隙太大,钝边太小时也容易出现烧穿现象。
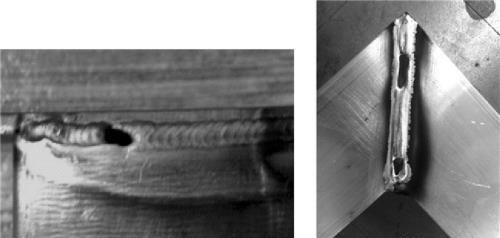
图3
(4)表面未熔合 未熔合是指焊缝金属与母材金属,或焊缝金属之间未完全熔化后结合在一起的缺陷,发生在焊缝表面的肉眼可见的未熔合缺陷称为表面未熔合,如图4所示。
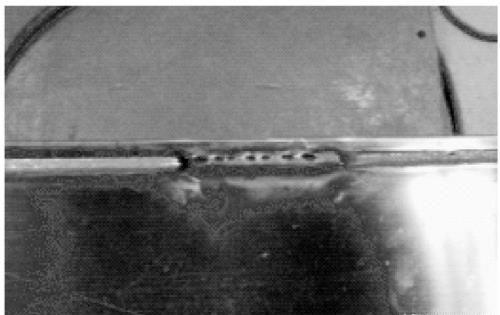
图4
(5)满溢 满溢是指熔化的金属太多流淌而出敷盖在焊道单侧或两侧的母材上,如图5所示。
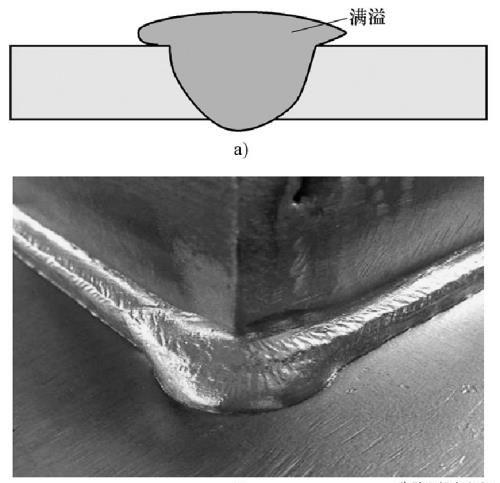
图5
(6)焊偏 焊偏在焊缝横截面上显示为焊道偏斜或扭曲,如图6所示。
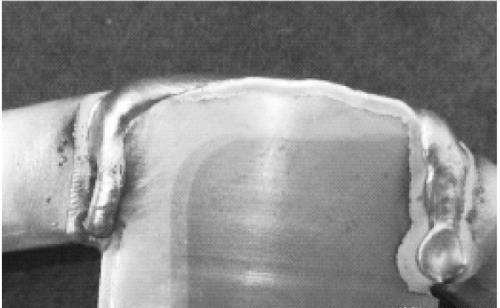
图6
(7)弧坑 电弧焊时,在焊缝末端收弧处或接头连接引弧处低于焊道基体表面的凹坑称为弧坑,如图6-7所示。在这种凹坑中很容易产生气孔和微裂纹。
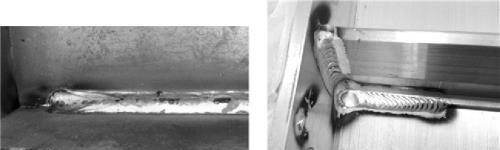
图7
(8)表面气孔 表面气孔是指焊接时,熔池中的气体未在金属凝固前逸出,残存于焊缝之中所形成的空穴,如图8所示。这里的气体可能是熔池从外界吸收的,也可能是焊接冶金过程中反应生成的。焊缝表面分布的气孔称为表面气孔。表面气孔多是由于焊接过程保护不良导致的。
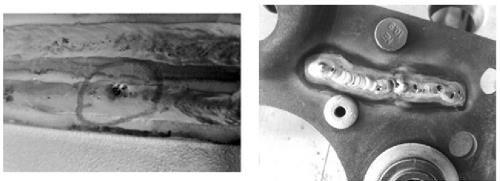
图8
(9)表面裂纹 表面裂纹是焊接过程中或焊接完成后,在焊接区域中出现的金属局部破裂的现象,如图9所示。
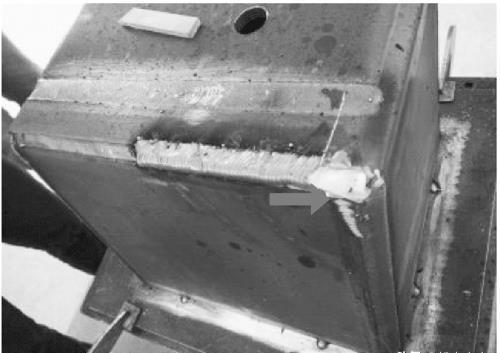
图9
2.焊缝内部缺陷
焊接时产生的气孔、裂纹、未熔合等缺陷,主要是出现在焊缝内部。
(1) 气孔 气孔是主要的焊接缺陷之一,常常发生在焊缝内部,如图10所示。焊件内部气孔多以氢气孔为主。焊前清理不当,焊材受潮,焊接参数不当等均有可能导致内部气孔产生。
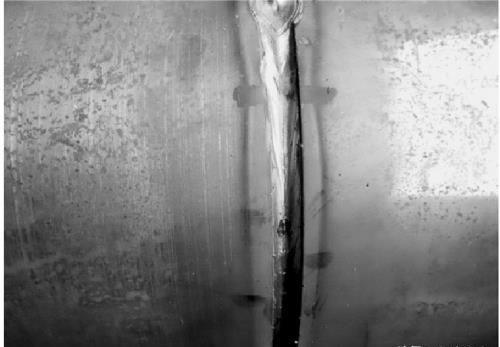
图10
(2) 裂纹 如上所述,裂纹是影响焊接质量的重大缺陷之一。发生于焊缝内部的裂纹称为内部裂纹,如图11所示。
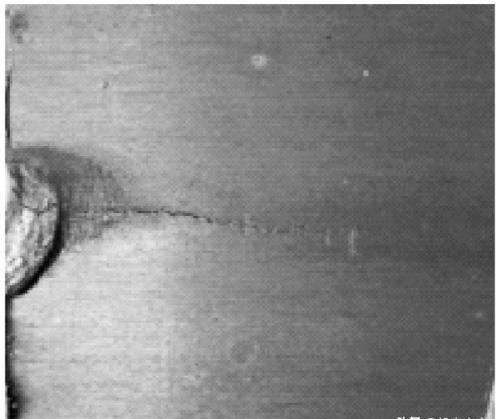
图11
二、机器人电阻点焊焊接缺陷的分类
电阻点焊焊点从外观上看,应达到外表面平整,无表面烧伤及烧穿缺陷,电极压痕不深,表面压坑深度一般不超过板厚的20%,且圆度好等要求。从内部看,应有尺寸合适的熔核,熔核应是很致密的铸造组织。
机器人电阻点焊与采用固定电焊机、手持式焊钳电阻点焊时的常见缺陷相同,按其所处位置不同,分为外观缺陷和内部缺陷。常见的外观缺陷主要有飞溅、毛刺、变形、漏焊、焊穿、焊点裂纹、焊点位置错误、压痕过深、粘铜等
机器人焊接缺陷产生的原因及其防止措施
一、机器人弧焊缺陷产生的原因及其防止措施
1.咬边
咬边缺陷通常发生在大电流高速焊接条件下,其形成的本质在于填充金属不能及时有效地填满焊缝母材凹陷。
(1)焊接电流大,焊接速度快
1)原因。焊接电流大,则熔化母材量大;焊速快,则熔化的焊丝不足,难以填满焊趾凹陷,从而易产生咬边缺陷,如图13所示。
2)防止措施。适当降低焊接电流和焊接速度,减小热输入,以防止产生咬边缺陷。
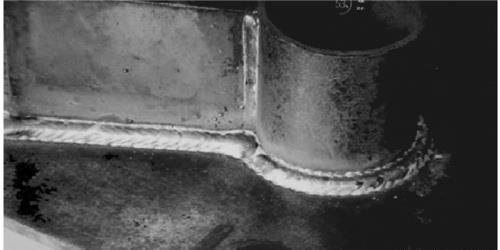
图13
(2)焊件温度高,影响焊接线能量
1)原因。如图14所示,容器上层方框体板厚为3mm,下层方框体板厚为10mm。
2)防止措施。改变焊接顺序,先焊立角焊缝(从上层至下层),然后分别从上层角焊缝往下焊至T形角焊缝(按上层角焊缝→上层T形角焊缝→下层角焊缝→下层T形角焊缝的顺序焊接)。
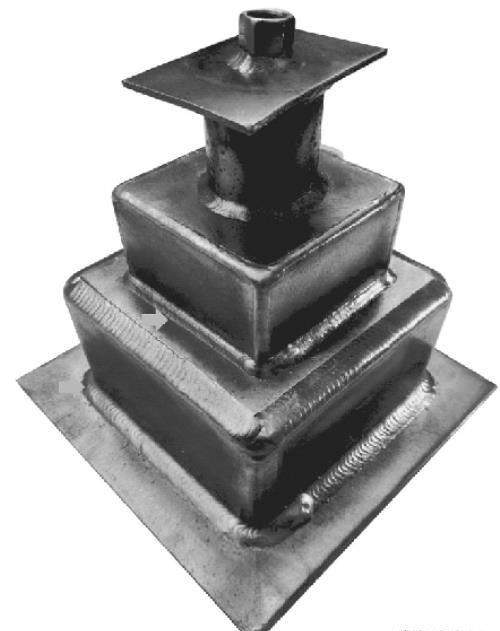
图14
(3)角焊缝编程时所选用焊接参数不当
1)原因。编程时采用直线摆动插补,摆幅上、下点选用了相同的焊接停留时间或焊接停留时间短,易产生咬边缺陷,如图14中的下层角焊缝所示。
2)防止措施。编程时选用直线摆动插补,振幅上点设置的焊接停留时间稍长于振幅下点。从而有效填充母材熔化的边缘,控制咬边缺陷的产生。
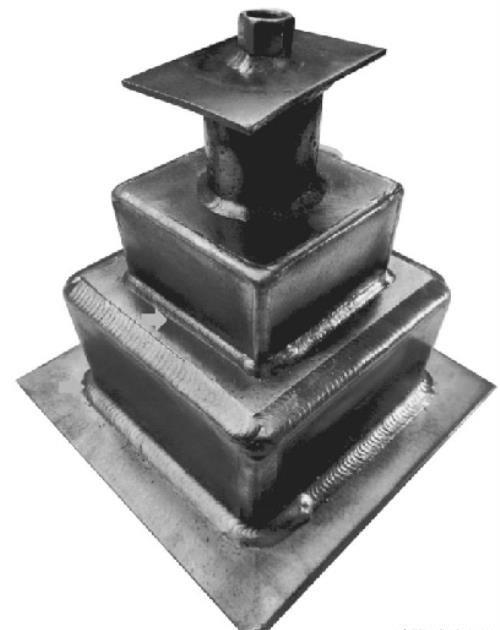
图14
(4)焊枪角度不当
1)原因。焊枪角度偏向底板使得电弧指向立板,造成局部能量集中,该处母材熔化量增多,而填充金属不够,造成咬边,如图15所示。
2)防止措施。一般焊枪轴线相对于焊接方向后倾约10°,与立板、底板之间的夹角为45°。
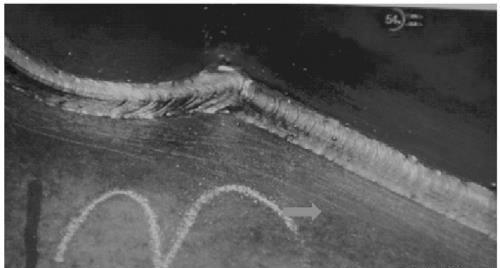
图15
(5)平对接V形坡口多层焊盖面焊缝咬边
1)原因。编程时设置的摆幅小且停留时间短,造成焊枪的焊丝末端摆动不到坡口边缘,被焊丝熔化的金属不能有效地填充母材熔化的边缘,从而形成了咬边缺陷。
2)防止措施。盖面前一层焊缝距离坡口端面约1mm,焊缝表面应光滑,编程时选用直线摆动插补,摆幅应稍大,以保证焊丝末端摆动到坡口边缘;振幅点设置的停留时间应稍长,以使熔化金属有效地填充母材熔化的边缘,从而防止产生咬边。
(6)送丝不稳定
1)原因。送丝不稳定将导致熔敷金属量不够连续稳定,造成局部位置填充金属不足,从而造成咬边缺陷。
2)防止措施。检查送丝系统,调整送丝轮压力,理顺送丝软管,勿使其发生大的弯折。
2. 未熔合
未熔合包括表面未熔合和内部未熔合。产生未熔合缺陷的根本原因在于局部热输入不够,以致填充金属与母材没有完全熔合焊接。
(1)管板接头引弧处易产生未熔合缺陷
1)原因。编程时设置的引弧参数不当,该处散热较快,从而造成焊接热输入过低,产生未熔合缺陷,如图16所示。
2)防止措施。该接头散热较快,编程时设置的引弧停留时间应稍长些,并适当增大焊接电流。
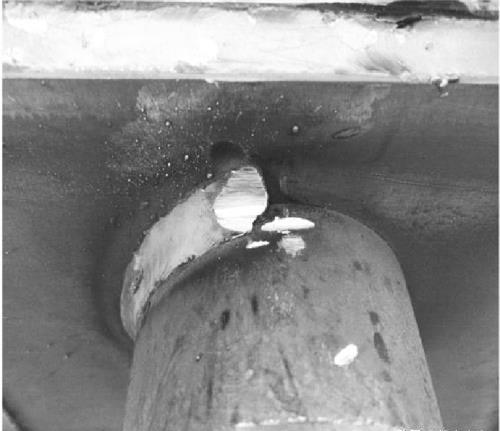
图16
(2)角接头90°转角处易产生未熔合缺陷
1)原因。圆弧插补设点不当易引起电弧指向偏离,电弧指向背离的一侧加热不足,易产生未熔合缺陷,如图17所示。
2)防止措施。编程时圆弧插补要结合焊件情况合理设点、设置焊枪角度和姿态,勿使电弧指向偏离。
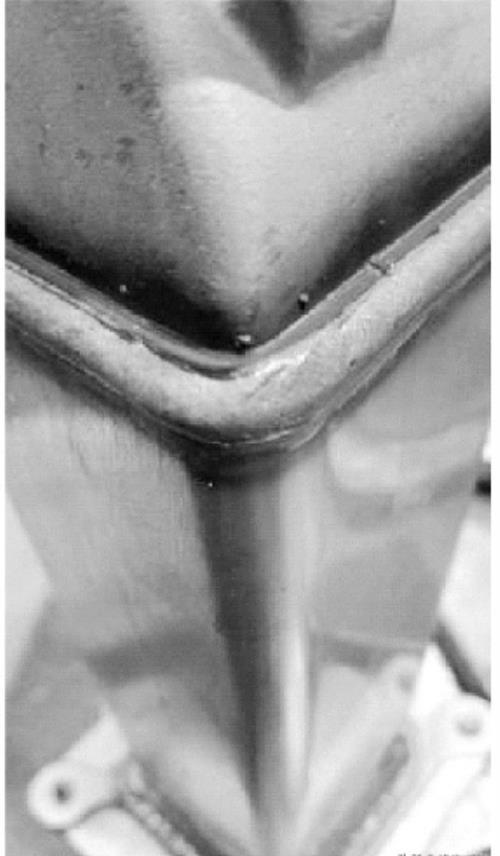
图17
3. 焊瘤
由于焊接电流过大,击穿焊接时电弧燃烧,加热时间过长造成熔池温度升高,熔池体积增大,液态金属因自身重力作用下坠形成焊瘤。焊瘤大多存在于平焊、立焊背面焊缝中,如图18所示。
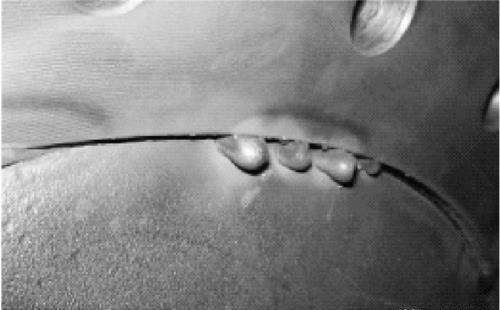
图18
(1)焊缝装配间隙大
1)原因。焊件下料加工精度差或焊缝装配间隙大,焊接时填充金属容易从间隙漏到焊缝背面形成焊瘤。
2)防止措施。根据焊件的技术要求,选用合适的下料加工方法来保证加工精度,尽量选用装夹具装配,保证装配精度,以防止产生焊瘤。
(2)焊件装配间隙为零,选用焊接参数不合理
1)原因。焊接参数大,焊接速度慢,此时焊缝易发生烧穿,且在背面熔敷金属将聚焦形成焊瘤。
2)防止措施。编程中设定焊接参数时应适当减小焊接电流或提高焊接速度。
(3)单面焊双面成形选用焊接参数不当以及焊丝端紧靠坡口边缘易产生焊瘤
1)原因。
① 直线摆动插补设置的摆幅左右两点停留时间长,造成局部热输入过大而容易形成焊瘤。
② 电弧熔化的金属在坡口边缘,易在背面形成熔敷金属聚集而产生焊瘤。
2)防止措施。编程时适当缩短摆幅左右两点停留的时间;焊枪的焊丝端适当向坡口边缘内靠。
4.烧穿
烧穿形成的机理是焊接热输入过大,焊接区域被完全熔透,且液态熔池整体失去有效支
撑而脱离,形成烧穿缺陷。应从熔池热输入和熔池支撑两方面来分析烧穿产生的原因和防止措施。
(1)薄板焊件选用焊接参数不当
(2)焊件间隙过大
(3)薄板搭接、T形角接焊缝焊接位置偏离
5.满溢
造成满溢的根本原因是填充金属熔敷过多而母材熔化不够,导致液态金属流淌堆积而形成满溢。
(1)T形接头90°转角焊缝易产生满溢缺陷
1)原因。在90°转角处,若编程时设置的圆弧轨迹点及选用焊接参数不当,则焊枪在转角旋转时,焊丝端部焊点(即焊接机器人TCP点)并未移动,热输入瞬时增大,熔敷金属增多出现堆积和外流,从而易产生满溢缺陷。
2)防止措施。编程时合理设置圆弧轨迹点,适当降低焊接电流或提高焊接速度,以防止产生满溢缺陷。
(2)外角焊缝易产生满溢缺陷
1)原因。焊枪中心偏离焊缝中心,焊枪向外偏离,可能会产生外侧满溢缺陷,如图21所示。
2)防止措施。保证焊缝示教精度,示教时焊丝干伸长保持为设定TCP点时的干伸长数值,焊枪中心对正焊接中心,以防止产生满溢缺陷。
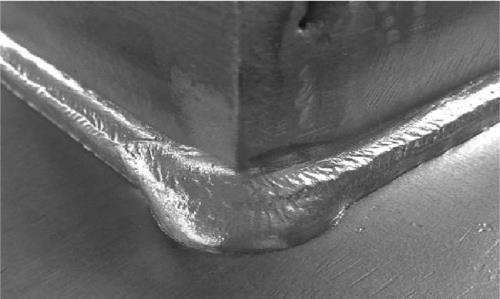
图21
6.焊偏
焊偏是指焊接轨迹偏离焊缝位置,主要原因是示教编程误差、工件装夹松弛、TCP点标定误差过大或TCP点丢失。针对这些原因,应分别采取不同的防止措施。
1)为防止出现示教编程误差,应尽量保持焊丝干伸长为标定TCP点时的数值;选择示教点时,应保证焊丝末端恰好接触到工件;调整视角,避免示教人员出现视觉误差。
2)为防止工件装夹松弛,应调整和紧固工装,避免工件变形和移动,适当减小热输入,抑制焊接变形或使用焊缝跟踪功能。
3)为防止机器人TCP点标定误差过大或TCP点丢失,以MIG焊为例,应保持焊丝干伸长为工艺规程确定的合适数值,按照标准五点法或四点法标定机器人TCP点参数。
7.气孔
气孔产生的机理是熔池中的气体不能及时逸出,熔池凝固时气体被固化在焊缝内部或表面而形成气孔。
产生气孔的主要原因:气体不纯,气路不通畅,气体流量不足,均会导致焊接区保护不良;焊枪角度不当,如焊枪角度过大,则会导致熔池保护效果不佳,易产生气孔;母材或填充焊丝受潮;MIG焊焊丝干伸长过大或TIG焊弧长过大,导致焊接区保护效果变差,有可能增加气孔敏感性。
8.裂纹
裂纹包括表面裂纹和内部裂纹。裂纹形成的机制比较复杂,影响因素比较多,主要原因如下:焊接热输入过大,导致裂纹敏感性增加;层间温度控制不合理,多层多道焊时,层间温度过高或过低都会引起裂纹;收弧填充不足,形成弧坑,从而引起弧坑裂纹。
免责声明:本站部份内容由优秀作者和原创用户编辑投稿,本站仅提供存储服务,不拥有所有权,不承担法律责任。若涉嫌侵权/违法的,请反馈,一经查实立刻删除内容。本文内容由快快网络小楠创作整理编辑!